Centrifugal Finishing Machine
SUPER FIN centrifugal finishing is a unique high energy mass finishing process. In this machine four barrels are mounted on the periphery of the roating turret.
As turret roates along its axis at high speed, centrifugal force is generated inside the barrels. These barrels are also rotated along its own axis (straight axis or skew axis) in opposite direction.
Each barrel contains media, finishing compound, water and parts to be finished.
Due to rotation of turret & barrel, media inside barrel rub against the parts under pressure. The high pressure sliding / rubbing action of media performs the surface finishing of the parts and reduces finishing time to just a few minutes from many hours.
SUPER FIN is ideally suited for high quality finishing. It can process even fragile & delicate parts without any distortion.
The loading device loads work pieces directly into the blast machine from containers, pallets or so-called charging baskets. The work pieces slide through the open loading door and onto the advancing caterpillar tread.
The loader subsequently returns to its initial position. The blasting process begins after the loading door is automatically closed and then locked. After the blasting period ends, the door opens automatically. The freshly blasted work pieces are removed in sequence by a take-off conveyor, or by emptying them directly into containers provided by the customer.
The blasting abrasive is continuously cleaned, recirculated and reused. An abrasive metering device feeds the cleaned abrasive from the abrasive storage bunker to the high-performance turbines.
A fan unit creates the partial vacuum necessary to maintain dust-free operation of the blasting unit. Extracted air is cleaned in a special filter unit.
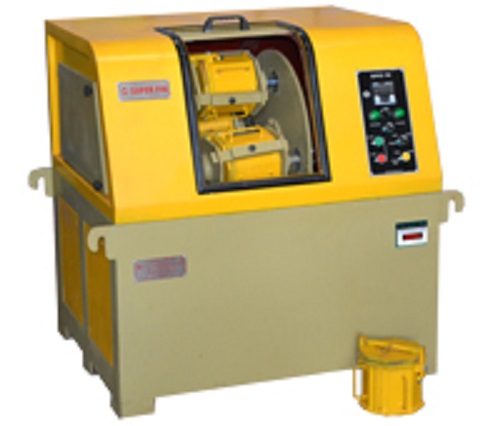
Why Choose Us
Gujarat Industries’s extensive plating and electroplating expertise enables us to offer unique product design, prototype and production capabilities to our valued customers. Advanced surface engineering processes, such as electroplating, are used to protect, improve the appearance, insulate; or increase the corrosion protection, conductivity, solderability, or modify the surface of the substrate material.
Our electroplating capabilities are specifically adapted for application-specific processes including: